Miriam Schuster,
Junior Research Group Leader Glass and Polymers
Glass in the building industry has long since ceased to be limited to classic windows. Ever larger glass formats are leading to almost completely transparent building envelopes. Ever thinner glass panes enable flexible structures. 3D printed glass elements enable new connection details. Vacuum insulating glass combines slim glass structures with good structural-physical properties. Glass-polymer laminates ensure residual load-bearing behavior in the event of glass breakage.
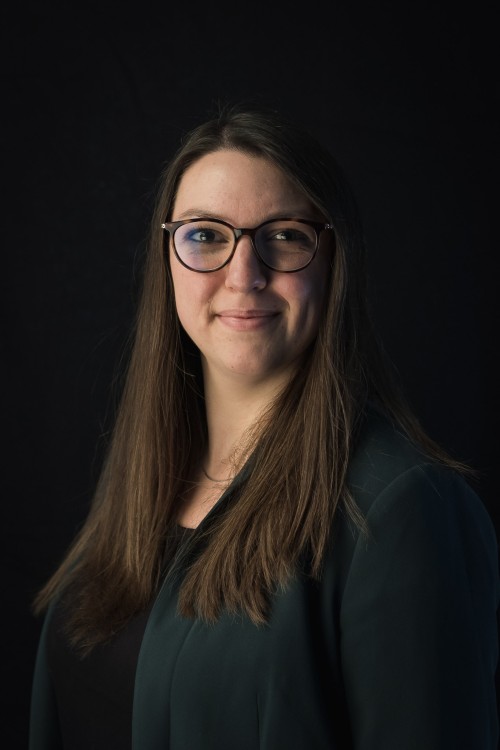
Main Topics
The Glass Competence Center brings together interdisciplinary expertise in materials development, quality assurance, sustainable construction, and digital technologies in glass engineering – ranging from innovative glass products and advanced joining techniques to forward-looking approaches such as circular economy and artificial intelligence.
The current research projects of the GAP team are:
Glass Products | Product Qualification | Polymeric Materials | Glass Strength and Quality | Sustainability | Other Topics |
---|---|---|---|---|---|
Laminated Safety Glass (LSG) | Testing – Monitoring – Certification | Glued All-Glass Constructions | Surface and Edge Strength | Reuse/Repurpose | Artificial Intelligence |
Insulating Glass Units (IGU) | Standardization | Polymeric Interlayers for LSG | Thermal Fracture | Remanufacture | Glass 3D Printing |
Vacuum insulating Glass (VIG) | Inclusions in Glass | Reduce | |||
Thin Glass | Tempered Glass | Recycle | |||
Photoelasticity and Anisotropy | |||||
Current Projects
- OpenFace / Micromaster
- Methodenentwicklung zur numerischen Abbildung des Nachbruchverhaltens von Verbundsicherheitsglas - NachbruchVSG
- CrackCut
- Entwicklung additiv gefertigter linienförmiger Verstärkungs- und Halterungsstrukturen aus Glas sowie formschlüssiger Beschläge - LinA
- Untersuchungen zur Wieder- und Weiterverwendung von Bestandsgläsern - ReUse
- Organisation Glasstec
- Detektion von Nickelsulfid-Einschlüssen bei der Flachglasbearbeitung - ProDeNiSE
- Entwicklung einer innovativen, rahmenlosen, selbsttragenden, thermisch isolierten und somit vollwertigen Glaskonstruktion für horizontale und vertikale Anwendungen - Rahmenlose Glaskonstruktionen
- Bruch- und Nachbruchverhalten von Glas- und Verbundglasstrukturen
- Requali VSG
Head
Name | Contact | |
---|---|---|
![]() | Dr.-Ing. Matthias Seel Head of Research Group Glass | seel@ismd.tu-... +49 6151 16-23015 L5|06 661 |
![]() | Dr.-Ing. Miriam Schuster Glass and polymers | Substitute professor in structural analysis (01.11.2023 - 31.03.2024) | schuster@ismd.tu-... +49 6151 16-23013 L5|06 628 |
![]() | Prof. Dr.-Ing. Michael Kraus Chair of Structural Analysis | kraus@ismd.tu-... +49 6151 16-23013 L5|06 620 |
Team
Name | Contact | |
---|---|---|
![]() | Isabell Ayvaz M.Sc. | ayvaz@ismd.tu-... +49 6151 16-23032 L5|06 607 |
![]() | Leon Bohmann M.Sc. | bohmann@ismd.tu-... +49 6151 16-23035 L506 626 |
![]() | Christin Gandyra M.Sc. | gandyra@ismd.tu-... +49 6151 16-23019 L5|06 632 |
![]() | Nils Meinhard, M.Sc. | meinhard@ismd.tu-... +49 6151 16-23014 L5|06 659 |
![]() | Franz Paschke M.Sc. | paschke@ismd.tu-... +49 6151 16-23062 L5|06 665 |
![]() | Dr.-Ing. Alexander Pauli | pauli@ismd.tu-... |
![]() | Dr.-Ing. Timon Peters | peters@ismd.tu-... +49 6151 16-23017 L5|06 609 |
![]() | Hans Ignacio Scholz Campos, M.Sc. | scholz@ismd.tu-... +49 6151 16-23014 L5|06 659 |
![]() | Kerstin Thiele M.Eng. | thiele@ismd.tu-... +49 6151 16-23014 L5|06 659 |
![]() | Dennis Behnoud M.Sc. | behnoud@ismd.tu-... L5|06 632 |
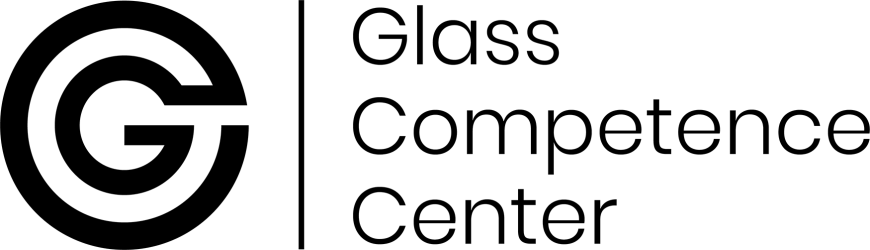
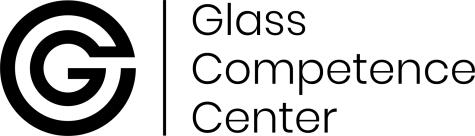