Recommended external content
We have selected external content from YouTube for you and would like to show it to you right here. To do this, you must reveal it with one click. You can hide the external content at any time with another click.
I agree to external content from YouTube being shown to me. This may result in personal data being transmitted to third-party platforms. You can find more information in our Privacy Policy.
Alexander Wolf,
Dr.-Ing. Architect, Head of the Generative Design Lab
3D printing and the construction industry: a technology and an industry made for each other. Compared to subtractive or formative manufacturing processes, additive manufacturing requires low investments that are affordable by the medium-sized enterprises in construction industry. The industry's products are unique, different for each building, and often complex.
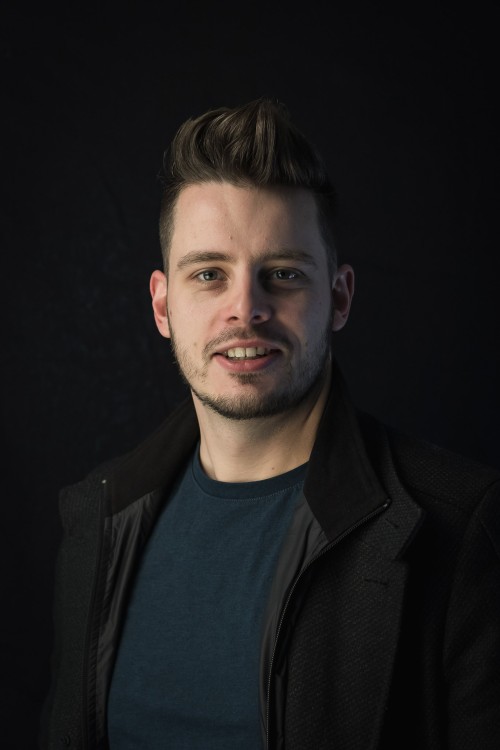
AM Ceramics describes the research of using clay as 3D printing material. Main topic is the development of the at ISM+D designed and built 3D clay-printing technology, based on an industrial Robot. This printer is used to examine potential applications for designing and constructing 3D printed bricks. Upcoming projects are the development of 3D printing techniques for restauration and conservation of old brick buildings and their facades. Moreover, the development of 3D printed pillars or supports with an interlock system are explored.
Head
Name | Contact | |
---|---|---|
![]() | Dr.-Ing. Architekt Alexander Wolf | wolf@ismd.tu-... +49 6151 16-23013 L5|06 639 |
![]() | Prof. Dr.-Ing. Ulrich Knaack | knaack@ismd.tu-... +49 6151 16-23036 L5|06 628 |
Team
Name | Contact | |
---|---|---|
![]() | Philipp Amir Chhadeh M.Sc. | chhadeh@ismd.tu-... +49 6151 16- 23019 L5|06 632 |
![]() | Christin Gandyra M.Sc. | gandyra@ismd.tu-... +49 6151 16-23019 L5|06 632 |
![]() | Marvin Kehl M.Sc. | kehl@ismd.tu-... +49 6151 16-23038 L5|06 414 |
![]() | Kerstin Thiele M.Eng. | thiele@ismd.tu-... +49 6151 16-23014 L5|06 659 |
![]() | Juan Ojeda M.Sc. | ojeda@ismd.tu-... +49 6151 16-21387 L5|06 414 |