Glas 3D Druck: Temperaturmessung beim Aufheizen und Abkühlen der Basisplatte und resultierende Spannungen
Bachelor thesis, Master thesis
To address the desire for transparent facades, glass 3D printing will be used to create novel joints for facade applications. Figure 1 shows the construction chamber of the glass 3D printer at the TU Darmstadt, which is to print molten glass onto a heated base plate made of glass.
To understand the process of glass 3D printing, the heating of the base plate using a hot plate and gas burner and the subsequent cooling will be studied. In order to know and reduce the risk of breakage during printing, temperatures and stresses during printing will be studied. For this purpose, a thermographic camera is available to measure the temperature of the glass surface, see Fig. 2b. Numerical simulations are possible to calculate stresses during heating. After cooling, residual stresses may remain in the glass, affecting the optical and mechanical quality of the component. The residual stresses can be studied after printing using stress optics, see Fig. 2a. Experiments on heating and cooling the base plate on the glass 3D printer can be carried out in a thesis.
Research objective
The aim is to be able to describe the heating and cooling of the base plate for glass 3D printing in terms of temperatures and stresses in the glass.
Research method
The research is based on literature and experiments.
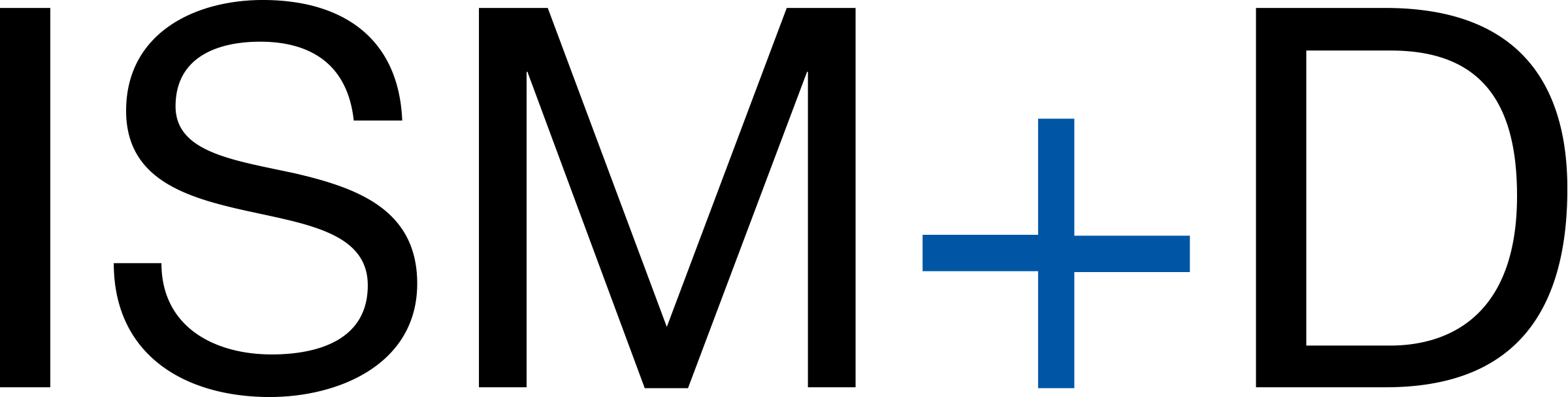